Empower Your Innovations
Leading Lithium Battery Equipment Supplier
Explore our range of high-quality lithium battery equipment designed to meet the unique power needs of your business. Let us help you drive efficiency and reliability in your operations.
What We Offer
Featured Services
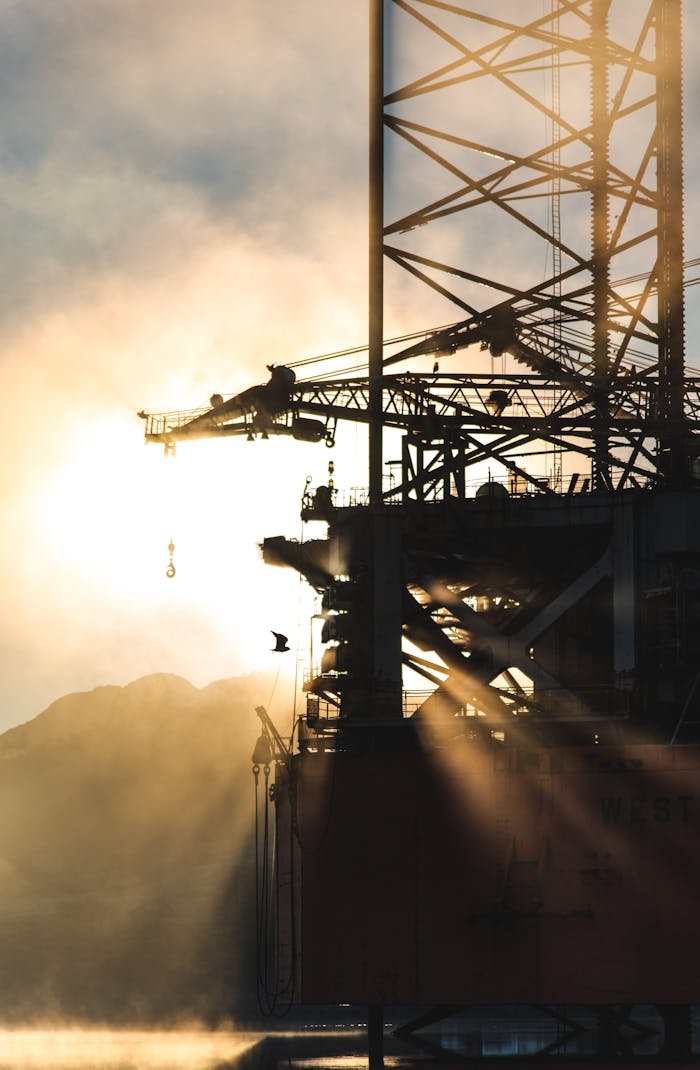
Equipment Sourcing
Source top-of-the-line lithium battery equipment tailored to your business needs for enhanced performance.
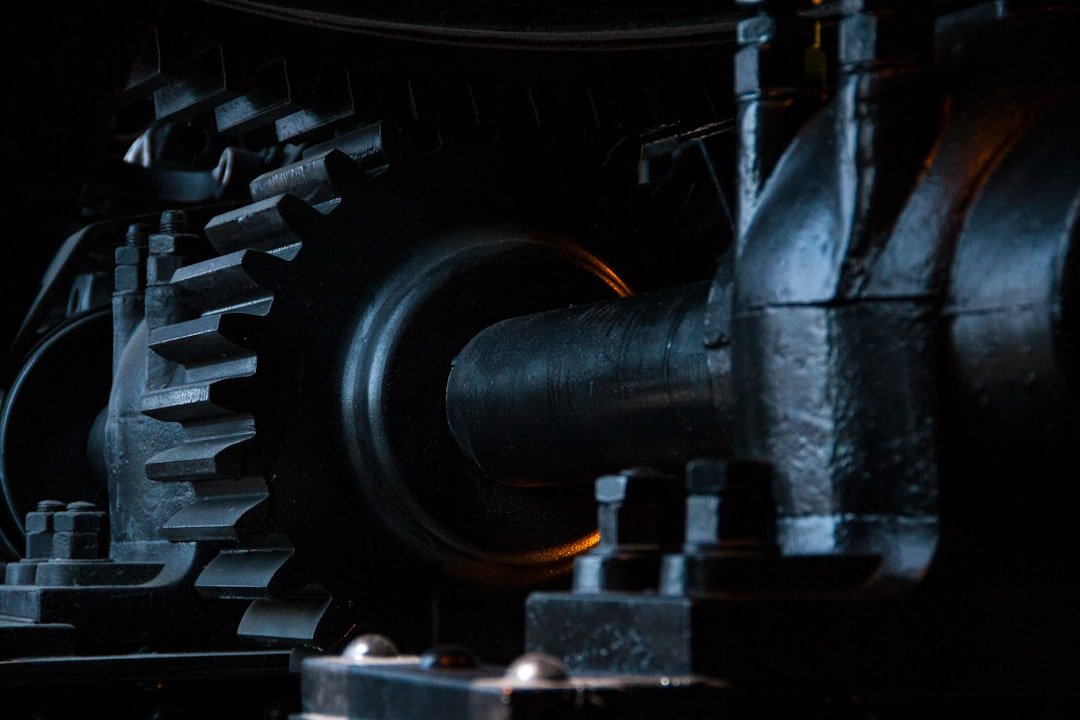
Custom Solutions
Get specialized solutions for your power requirements with custom-designed lithium battery equipment.
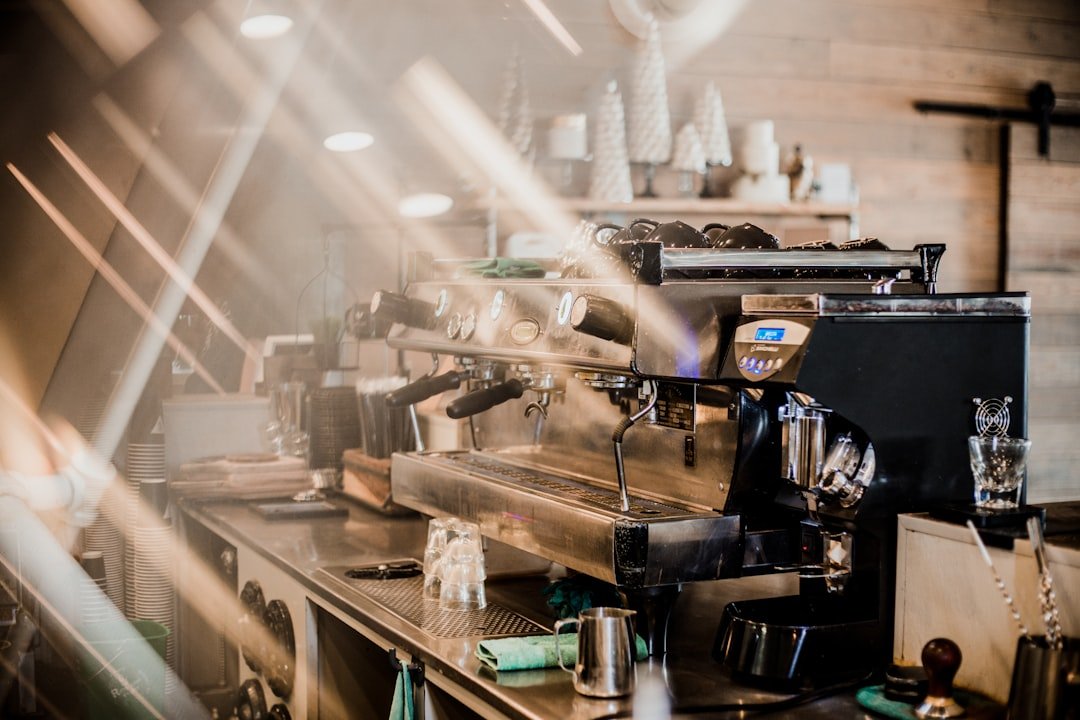
Efficiency Expertise
Improve operational efficiency with our expertly crafted lithium battery equipment designed for reliability and performance.
Why Choose Us
Our Unique Value Proposition
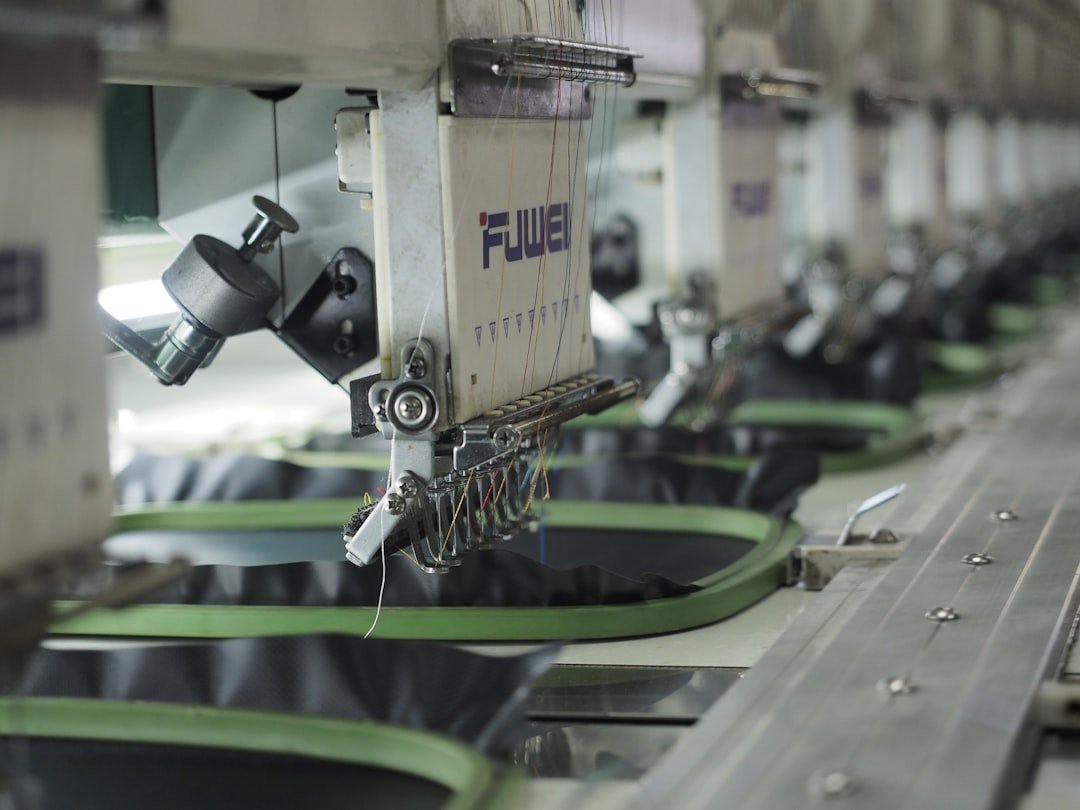
Power Up Your Business Today
Discover our cutting-edge lithium battery equipment designed to fuel your entrepreneurial endeavors.
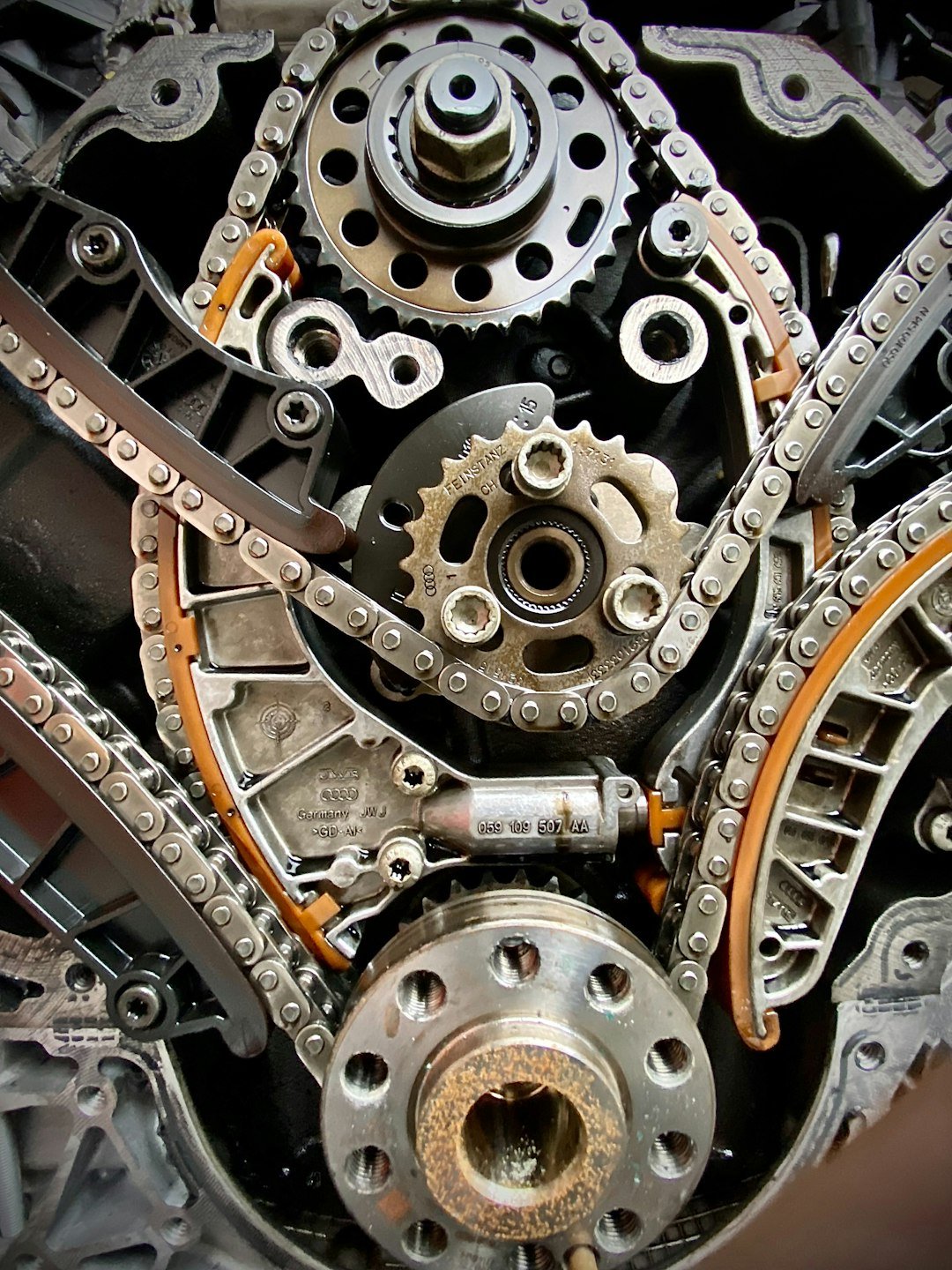
Our Story
Empowering Innovations Since 2010
PowerTech Solutions is dedicated to providing top-quality lithium battery equipment tailored to meet the unique needs of businesses. We support entrepreneurs in powering their ventures with the latest technology.
Explore Our
Gallery
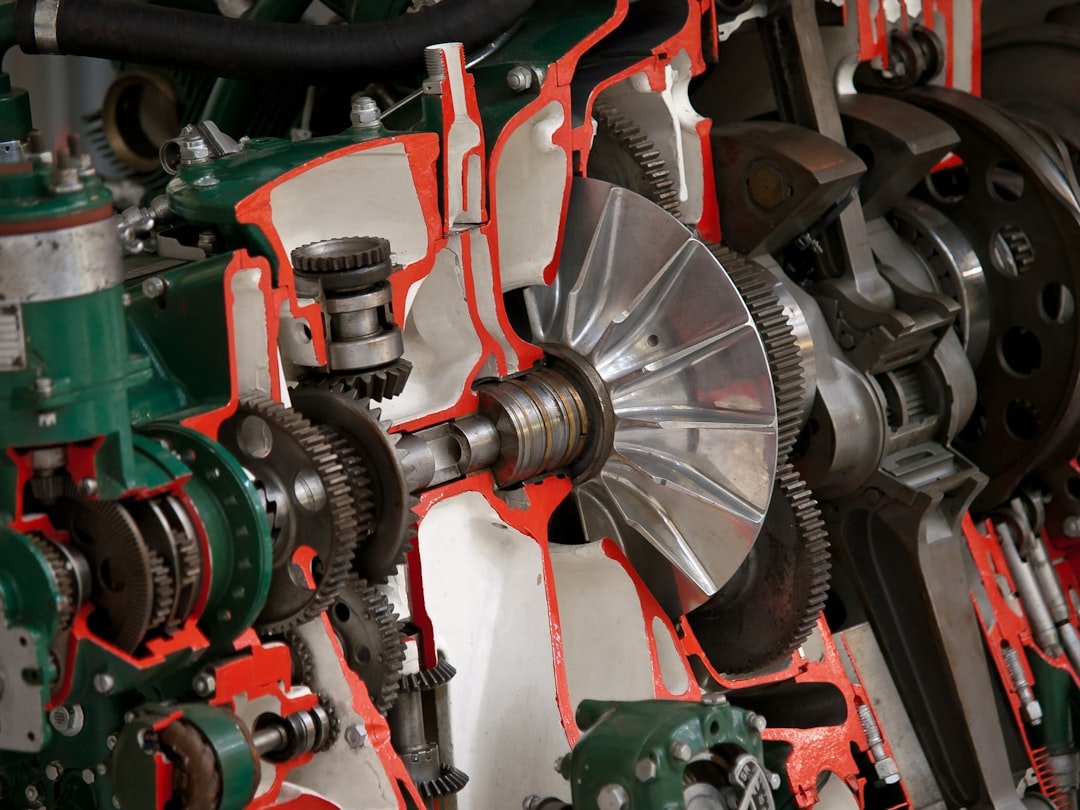
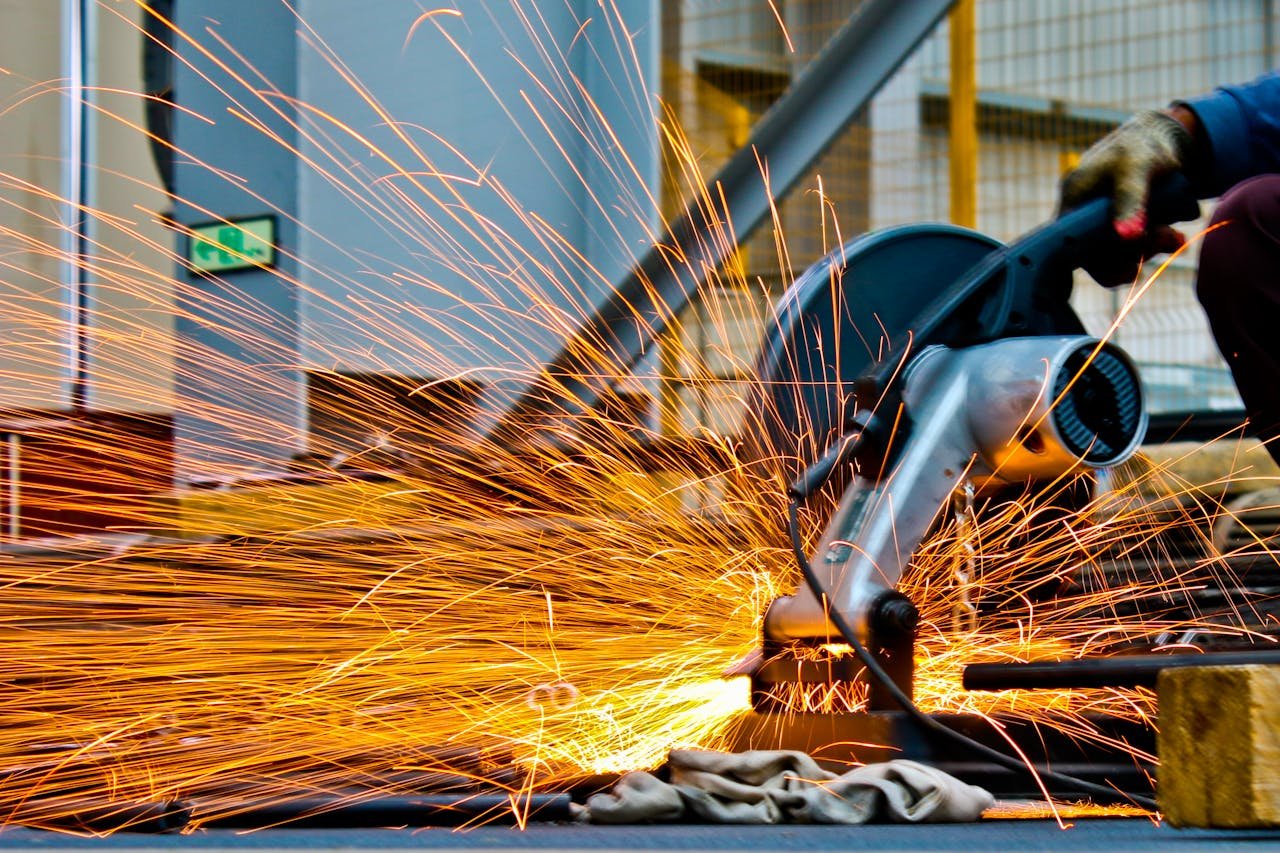
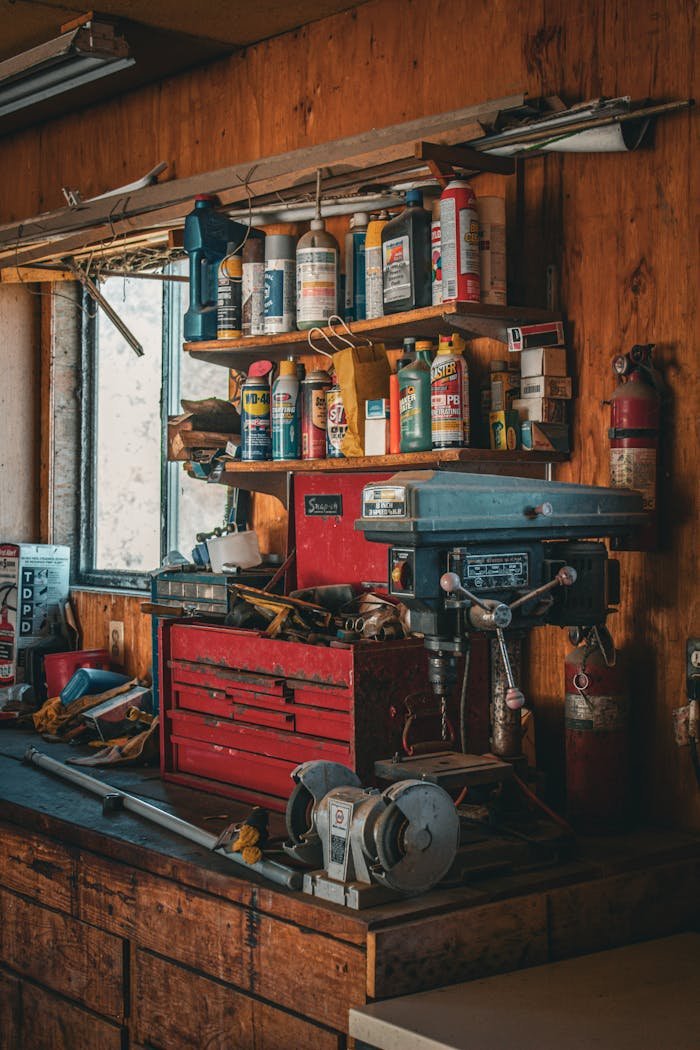
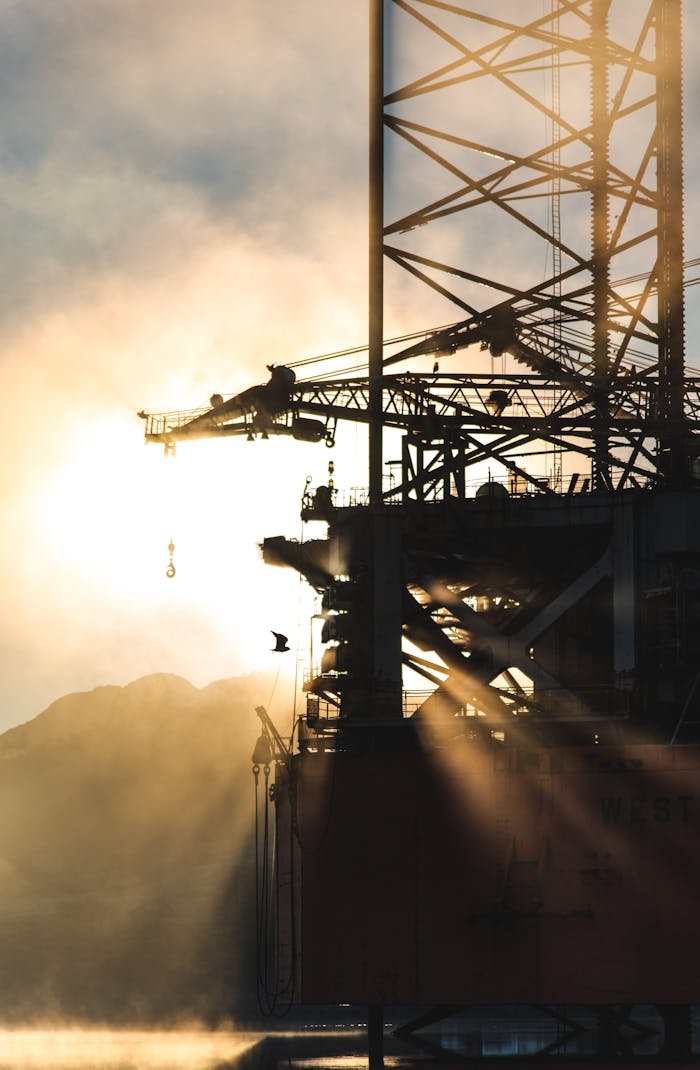
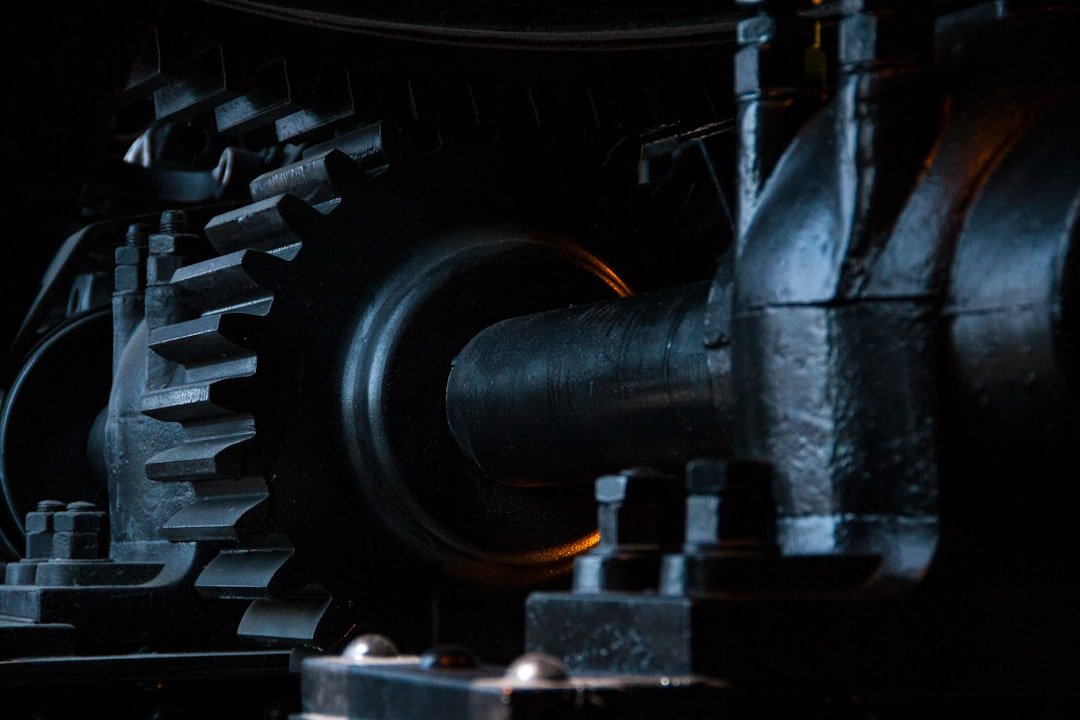
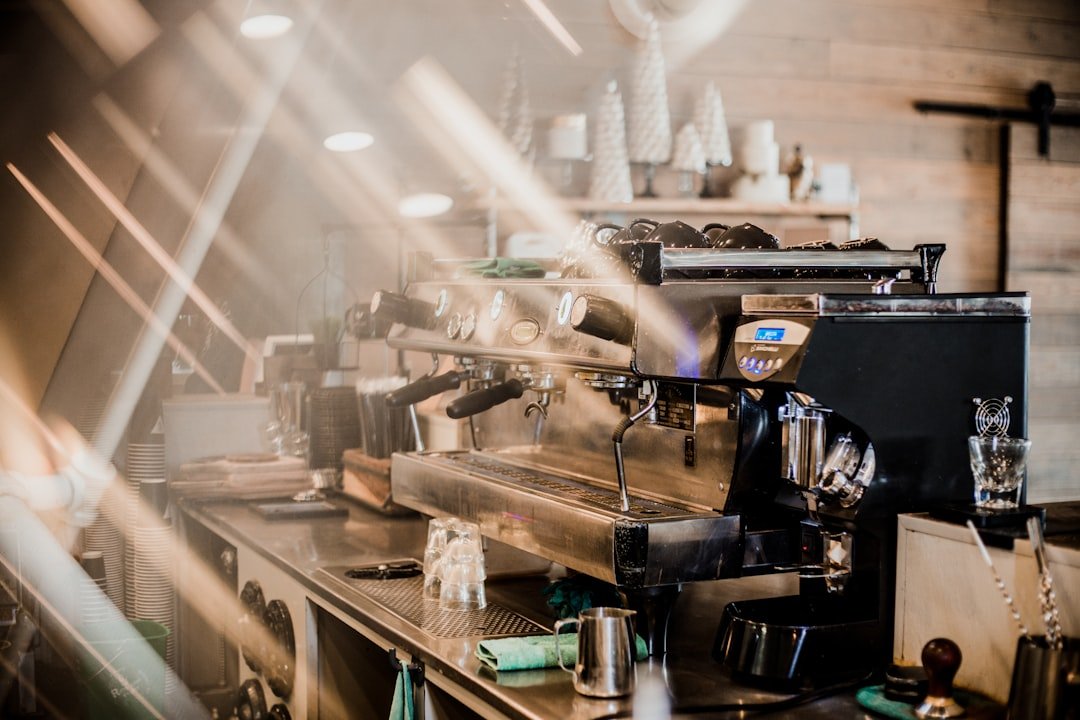
Client Stories
Testimonials
PowerTech Solutions provided us with exceptional lithium battery equipment that has boosted our productivity 10-fold. Highly recommended!

John Smith
I am amazed by the reliability and efficiency of the lithium battery equipment from PowerTech Solutions. It’s a game-changer for our business!

Emily Johnson
PowerTech Solutions has truly revolutionized our operations with their high-quality lithium battery equipment. Outstanding service!

Sarah Brown
Stay Ahead with Our Solutions
Contact us today to explore how our lithium battery equipment can power your innovations.
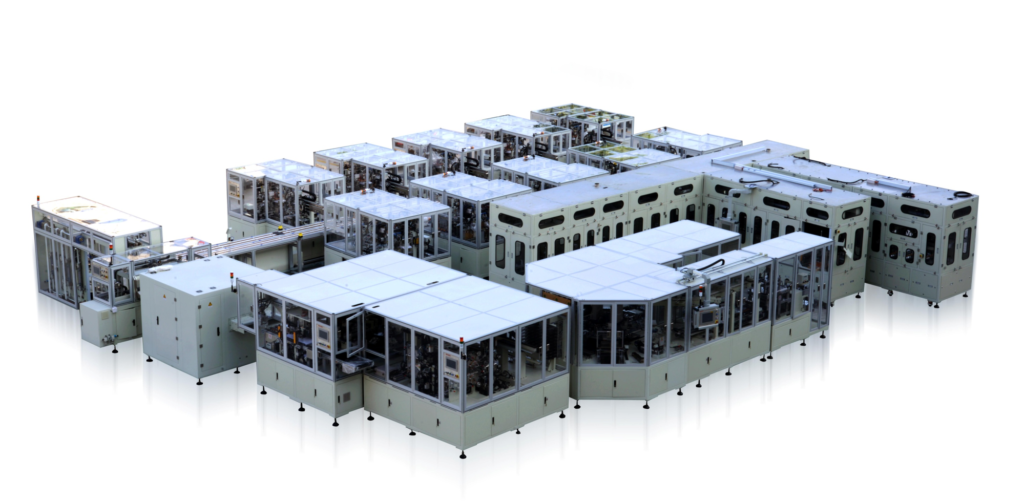
Introduction to the production process of lithium batteries in the laboratory
Material preparation
Positive/negative electrode materials: such as lithium cobalt oxide (LCO), ternary materials (NCM), graphite, etc., need to be ground to micron level (particle size ≤ 10 μm).
Electrolyte: commonly used LiPF6/carbonate solution, water content needs to be <20 ppm.
Current collector: aluminum foil (thickness 10-20 μm) for positive electrode, copper foil (8-15 μm) for negative electrode.
Electrode preparation
Slurry preparation: active material, conductive agent (such as Super P), binder (such as PVDF) are mixed in proportion (such as 90:5:5), and solvent (NMP or water) is added to stir into a uniform slurry.
Coating and drying: The slurry is evenly coated on the current collector (wet film thickness 100-200 μm), vacuum dried at 80-120℃, and the solvent is removed.
Roller pressing and slitting: Use a small roller press to compact the electrode sheet (positive electrode 2.5-3.5 g/cm³) and cut it into the required size (such as 20×20 mm).
Battery assembly
Stacking/winding: Manual stacking is commonly used in the laboratory. The positive electrode, separator (such as Celgard), and negative electrode are stacked in sequence, and the alignment error is less than 0.5 mm.
Packaging and injection: Pack soft pack or button batteries in a glove box (H₂O/O₂<1 ppm), inject electrolyte (2.5-3.5 g/Ah), and let it stand for 12 hours to soak.
Sealing: The soft pack battery is sealed with a heat sealer (temperature 150-180℃) to ensure no leakage.
Activation and testing
Formation: Charge to 3.0V with a small current of 0.02C for the first time to form an SEI film.
Cycle test: 0.5C charge and discharge, record capacity, efficiency and attenuation data.
Characterization and analysis: SEM was used to observe the electrode morphology, XRD was used to analyze the crystal structure, and EIS was used to test the interface impedance.